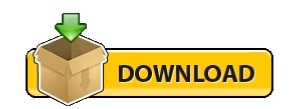
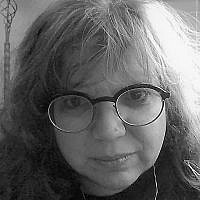

On the other side, IronCAD’s innovative parts have the unique capability of allowing both features and direct edit modifications to mix together, regardless of the feature history order or dependencies.īoth modes use the same modeling tools in creating geometry.IronCAD’s structured parts allow the traditional feature history to be created, along with direct edit modifications, which appear in the history order.It allows parts to be started in structured mode (equivalent to “ordered” in Solid Edge) or innovative mode (somewhat similar to “synchronous”) – we don’t have to decide. IronCAD is similar to the later releases of Solid Edge. Subsequent releases fixed the limitation, and now both techniques can be used at the same time. When Siemens PLM added Synchronous Technology to Solid Edge, the first two releases required users to decide right at the beginning of a new design whether to model the part with traditional techniques (ordered) or to use synchronous techniques a part could not have both ordered and synchronous features. I think you’ll find the similarities remarkable. In this article, I’m going to dissect some of the main features of Solid Edge’s Synchronous Technology and compare them with IronCAD.
HOW DO YOU CHANGE A SOLID EDGE FILE FROM SYNCHRONOUS TO ORDERED SOFTWARE
Lesser known is IRONCAD, the makers of the IronCAD Design Collaboration Suite, who began developing hybrid software in 1998, years earlier than any other vendor. Of the hybrids, the most notable ones are Solid Edge and NX from Siemens PLM that use a combination of synchronous and ordered environments within the same part file. While some vendors busily wrote distinct applications, others merged technology through a hybrid approach. Siemens PLM has had their Synchronous Technology, Autodesk their Fusion, and Dassault Systemes their V6 – along with lesser players. PTC’s CoCreate had employed the technology since the 1990s. Several vendors have been working at adding direct editing functions to their history-only modelers. SpaceClaim was probably the last software vendor to make the CAD world rethink the possibility of direct modeling. The second language seems different, but similarities become evident with the third and fourth languages. I have said that learning new CAD software is like learning a new language: the vocabulary and grammar may be different, but the concepts are the same. Synchronous Technologyįrom the blue gradient of the background to the uniformity of the ribbon bar, there is something eerily familiar to every MCAD software. Use the “Convert to Sheet Metal” command on the new solid body.IronCAD’s Hybrid Modeling Vs. Use the “Thicken” command on extracted surfaces. Activate the “Sew” command and sew all extracted surfaces. Select faces on the same side of the body. Hide first solid body and use “Convert to Sheet Metal” command on the new body. Set thickness value as a sheet metal thickness. Use the “Thicken” command and set face rule as a “single face. Trick 1: If you have problems transforming the solid body to sheet metal. After check model, delete the “Unbend“ command from the part navigator. If it is work, you transform a solid body to a “sheet metal body” successfully. Check sheet metal solid body by using the “Unbend “ command.Check solid body wall thickness or edges. If the model is not suitable for making sheet metal.Click MMB (middle mouse button) or “Ok” to finish.(Round, Square, None) I prefer to use “Round” Define “Bend Relief” in the “Relief” tab.(This base face will be the main face when sheet metal flatten.) Activate the “Convert to Sheet Metal” command.On the contrary, command gives an error message (The body has a non-uniform thickness or contains edges that need to be ripped. First of all, all of the solid body wall thickness should be the same thickness.Activate command from “Menu => Insert => Convertįor making sheet metal model from the solid body by using “Convert to Sheet Metal “ command:.Application activated.) “ Home => Basic Group => Convert Drop Down => Convert
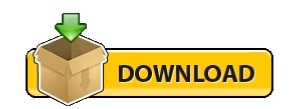